How to create and use a value stream map? A value stream map is an exhaustive process map of the relationships between the elements that create value for your customer — from beginning to end — from idea to revenue. Although this sounds simple, it is not. The only way to create such a map is with a complete cross-functional team of all of the folks involved in creating and delivering the value. Typically this effort is led by a trained facilitator with experience in creating value stream maps.
This is best done in a conference room with a large white board. A blank wall with a large number of easel pad sheets and a magic marker also works. It is important to not let anything constrain the creative process. If you need more space, figure out how to add it.
Value stream maps really require a cross-functional team with all of the functions represented. A very large part of the mapping process involves documenting the handoffs between functions or tools, so representatives of all the handoffs are necessary.
Most of the opportunity to streamline a value stream is in the function-to-function handoffs.
Mapping rules
Use standard flowcharting symbols and conventions as long as everyone is familiar with them. Don’t stop drawing until the map is done. Don’t be constrained by board or paper size. Figure out how to continue the process of capturing the flow.
Try to get the map done in one session of no more than 2-3 hours. The team facilitator should stay after to copy and refine the map and maybe redraw it using an automated mapping tool like Lucidchart.
At the end of the mapping process while the whole team is assembled and engaged, add time to the map. Using the team consensus add a time figure to each block in the map. A conditioned range of figures may be the most appropriate way to capture this information.
The whole team should review and verify the redrawn map. Once the map is complete and verified, the real work of value stream management can begin.
Also watch, How you can improve software delivery and optimize value streams using systems thinking and lean principles.
Value Stream Management
The value of a value stream map is in its usefulness for continuous process improvement. A value stream map is never done; it is always a work in process.
Potential areas of a value stream map to improve: manual hand-offs, undocumented procedures, storage areas, manual labor, overproduction and excess capacity, waiting, inventory, unnecessary movement, transportation, extra processing, retesting, resource underutilization, defects, anything that doesn’t add value to the customer.
These process improvement areas were first highlighted in the lean manufacturing revolution whose roots stretch back to the early Ford Motor Company through Demming in Japan and the rise of the Toyota Motor Company and the Six Sigma Manufacturing Movement. Only now these same principles are being successfully applied to software-based products.
If you need to understand more about value stream mapping and value stream management, contact us.
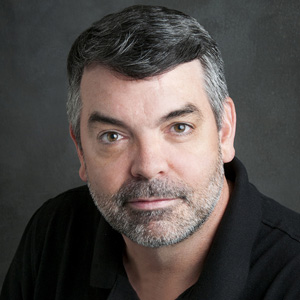
Lance Knight is the President and Chief Operating Officer of ConnectALL. His responsibilities include sales, sales operations, customer success, and technical support. Previously, he held SVP/VP roles at LeadingAgile, Tasktop Technologies, and Accept Software, specializing in field operations, sales development, and customer success. Lance started his IT career with a large aerospace manufacturer where he learned about Lean Manufacturing and Systems Thinking. He’s a published author of books and white papers on leadership, software development, and software sales.